it manufacturing cost of the first product would be 531, $29, $32, $28, and $29 in Plants 1, 2, 3,4, and 5, respectively. The unit manufacturing cost of the second product would be S45, S41, 546, $42, and $43 in Plants 1, 2, 3, 4, and 5, respectively. The unit manufacturing cost of the third product would be S38, S35, and $40 in Plants 1, 2, and 3, respectively, whereas Plants 4 and 5 do not have the capability for producing this product. Sales forecasts indicate that 600, 1,000, and 800 units of products 1, 2, and 3, respectively, should be produced per day. Plants 1, 2, 3, 4, and 5 have the capacity to produce 400, 600, 400, 600, and 1,000 units daily, respectively, regardless of the product or combination of products involved. Assume that any plant having the capability and capacity to produce them can produce any combination of the products in any quantity. Management wishes to know how to allocate the new products to the plants to minimize total manufacturing cost. (a) Formulate this problem as a transportation problem by constructing the appropriate parameter table. (b) Obtain an optimal solution.
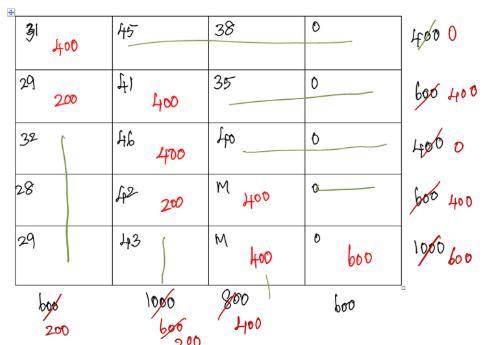